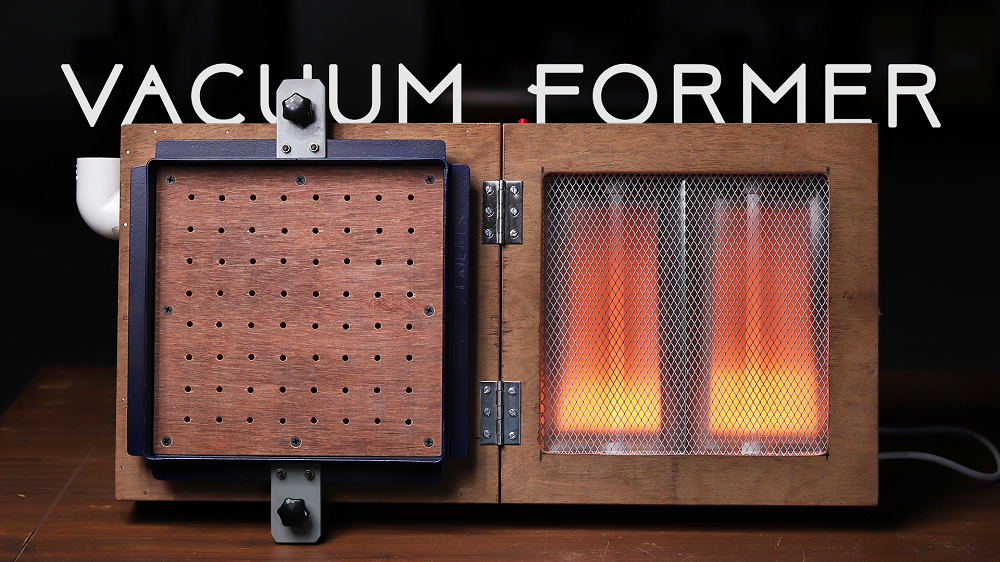
INTRODUCTION :
DIY Vacuum Forming Machine :
Vacuum forming is a simplified version of thermoforming, where a sheet of plastic is heated to a forming temperature, stretched onto or into a single-surface mold, and held against the mold by applying a vacuum between the mold surface and the sheet. This process is widely used to create a variety of products, from packaging to industrial components.
Here’s a step-by-step guide to building a vacuum forming machine using plywood, room heater parts, a vacuum cleaner, and L-angles, along with a description of the parts:
Parts Used :
- Plywood Frame:
12mm Plywood 12”*24” for base of the frame
2 Nos.12mm Plywood 2.5”*24” for side wall
2 Nos. 12mm Plywood 2.5”*12” for side wall
2 Nos. 12mm Plywood 12”*12” for upper parts of the frame
-
- This forms the main structure of the machine, providing a stable platform for the heating and vacuum forming processes.
- It will be used to create the box for the vacuum chamber, and also to create the frame to hold the plastic sheet.
- Room Heater Parts:
- In amazon site the heating tubes price is higher so I decide to purchase the Room heater, where I get all the required parts.
- Heating Tube: This will be the primary heat source for softening the plastic sheet.
- Safety Net: This is crucial for preventing direct contact with the hot heating tube, ensuring safety.
- Body and switch: Parts of the room heater body can be used to help mount the heating elements, and to help direct the heat.
- Vacuum Cleaner:
- This provides the vacuum force necessary to draw the softened plastic sheet down onto the mold.
- ¾ inch L-Angles:
- These will be used to create a frame that securely holds the plastic sheet during the heating and forming processes.
- Other Materials:
- Screws, glue, wire, 6mm knobs, and Hinges.
How to make :
- Construct the Vacuum Chamber:
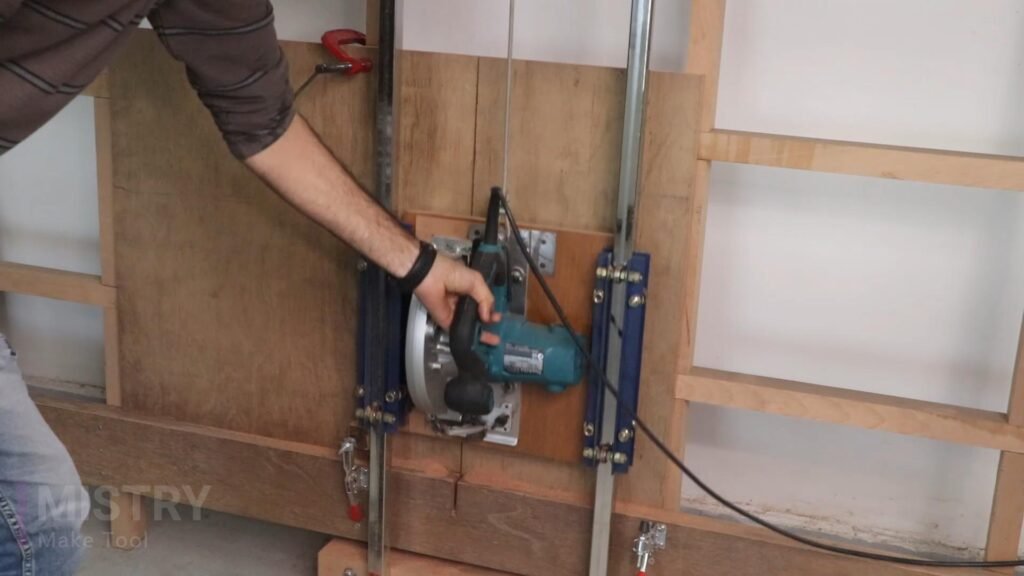
Cut plywood pieces to the desired dimensions for the base and sides of the vacuum chamber.
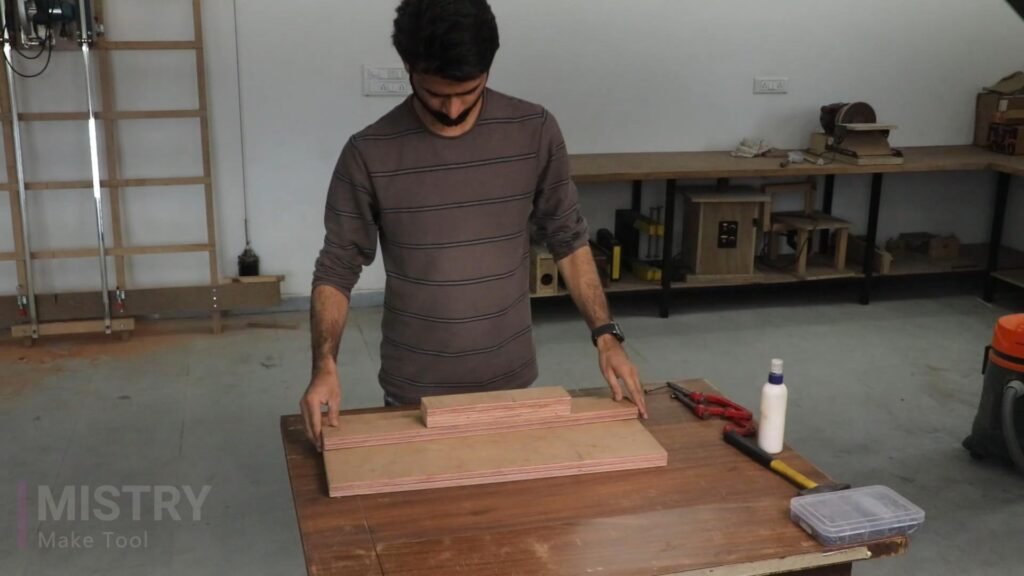
Assemble the plywood pieces to create a box-like structure. Ensure the seams are airtight. You may want to use sealant on the inside seams. I have used fevicol.
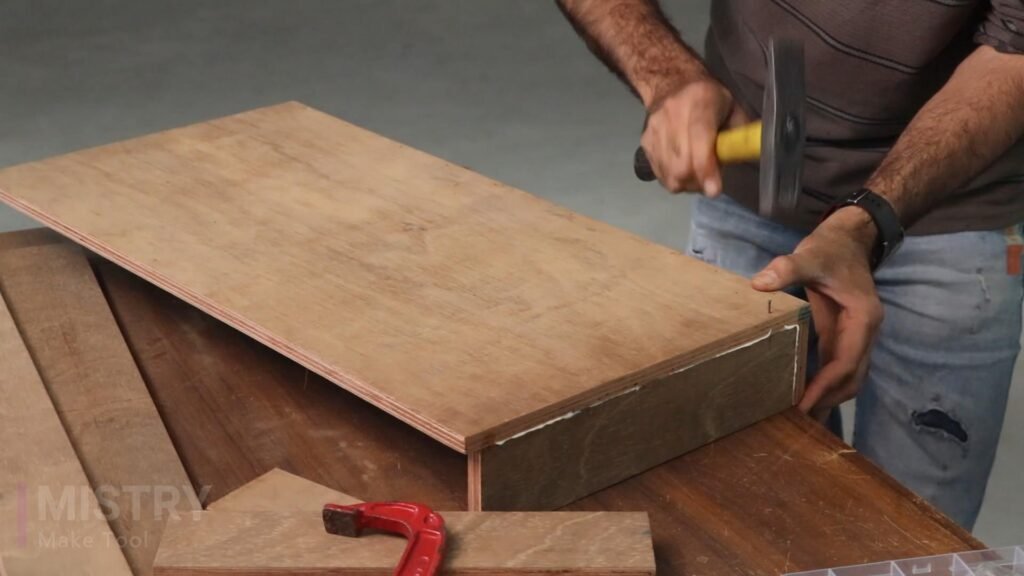
I separated this structure from the plywood wall. One part is for the vacuum chamber, and the second part is for the heating unit.
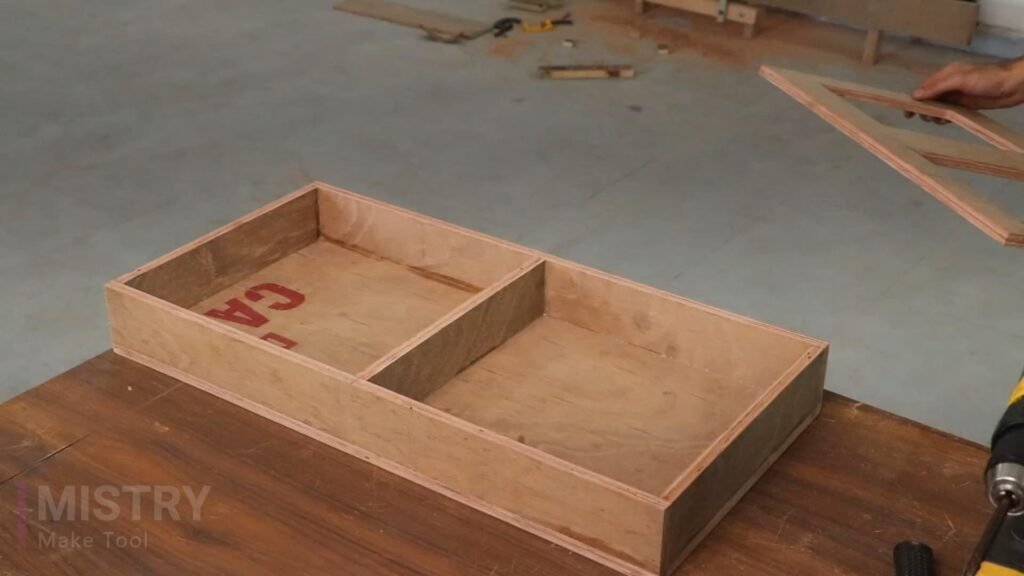
Drill a hole in one side of the box to accommodate the vacuum cleaner hose.
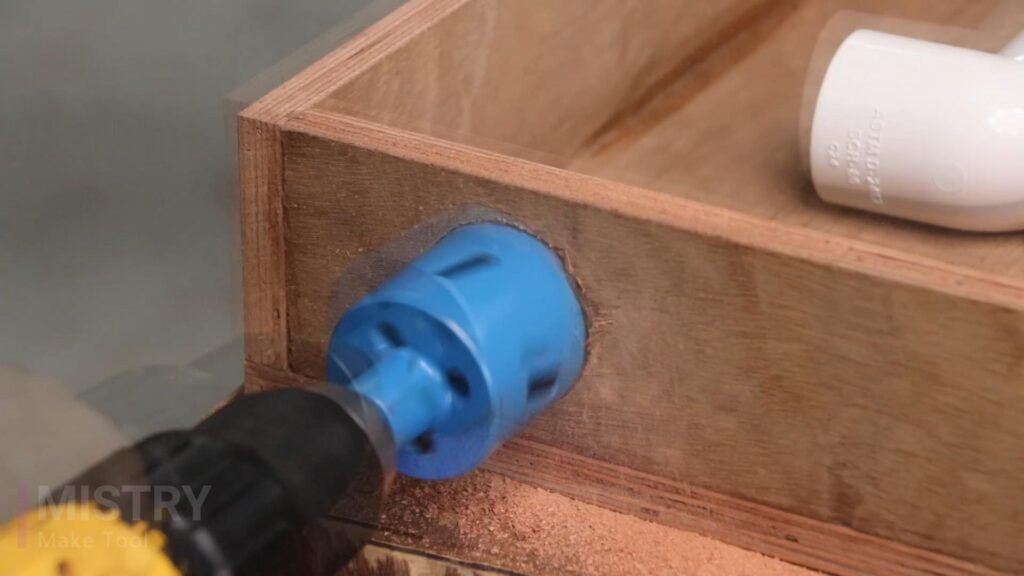
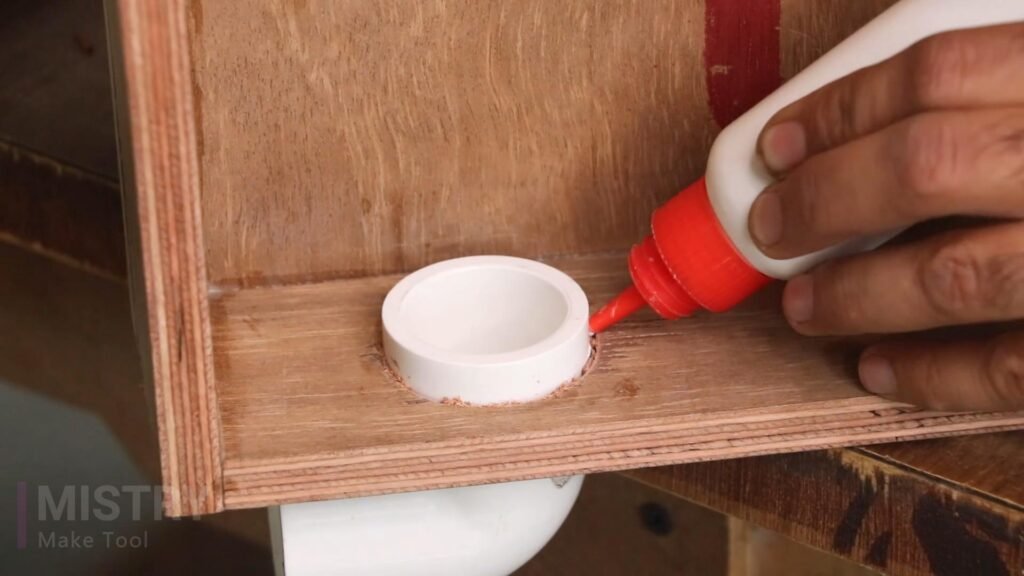
2. Build the Heating Unit:
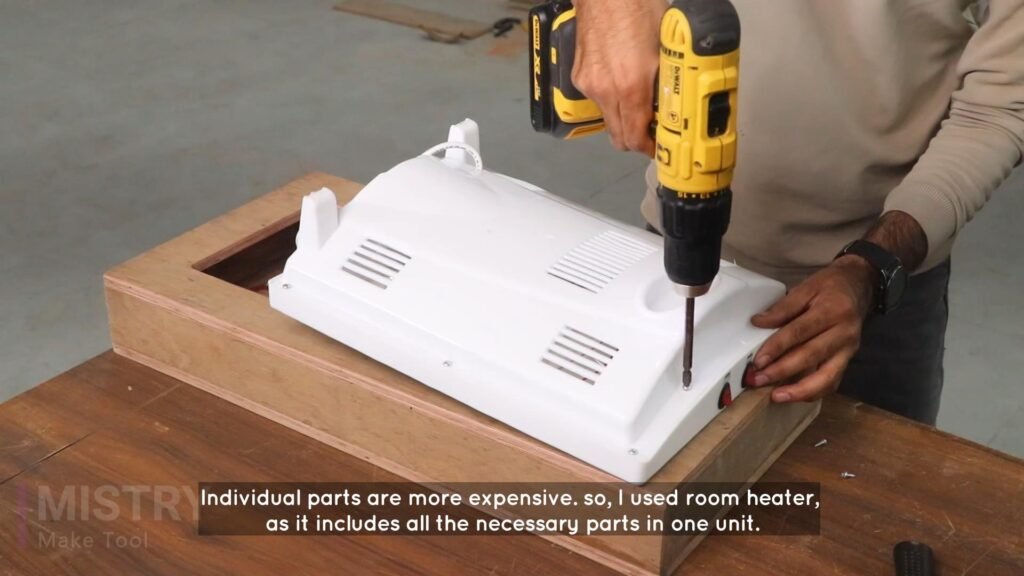
Mount the heating tube and safety net within a frame. This frame can be made from plywood. Ensure the safety net is positioned to prevent any contact with the hot heating tube.
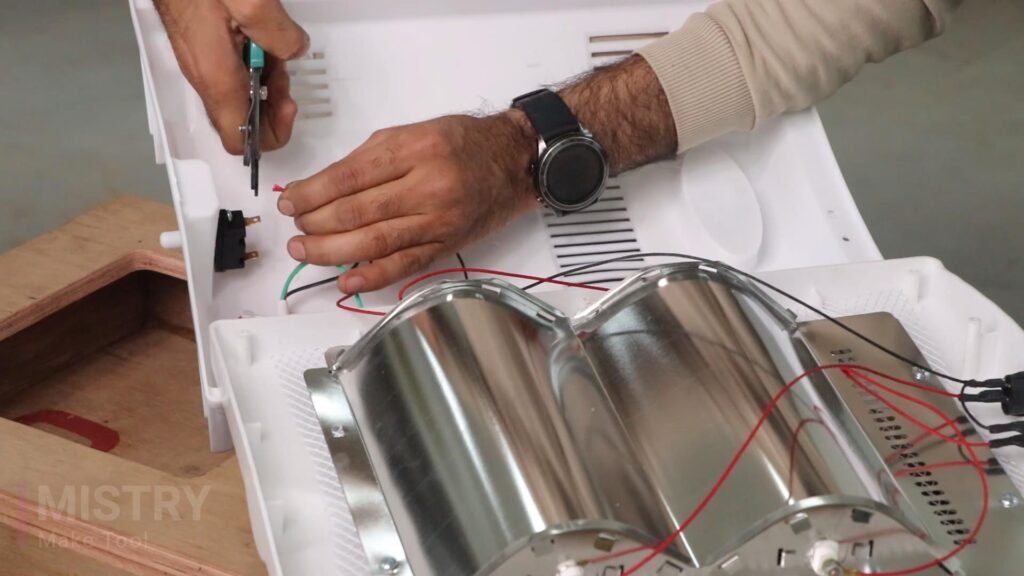
Wire the heating tube to a power supply, ensuring all electrical connections are safe and secure. If you are not experienced with electrical wiring, please seek the help of a professional.
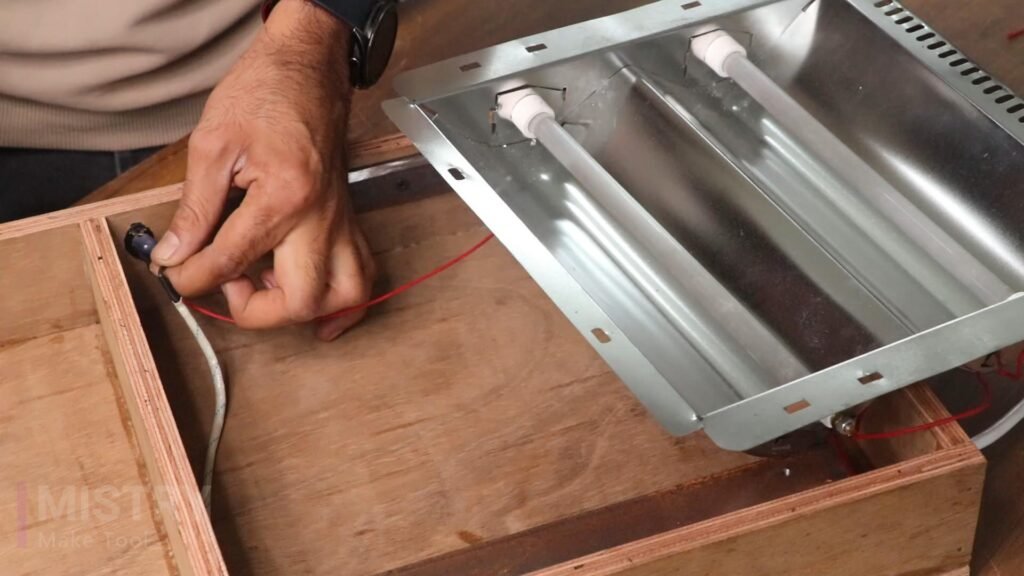
3. Top Parts For Work piece Base:
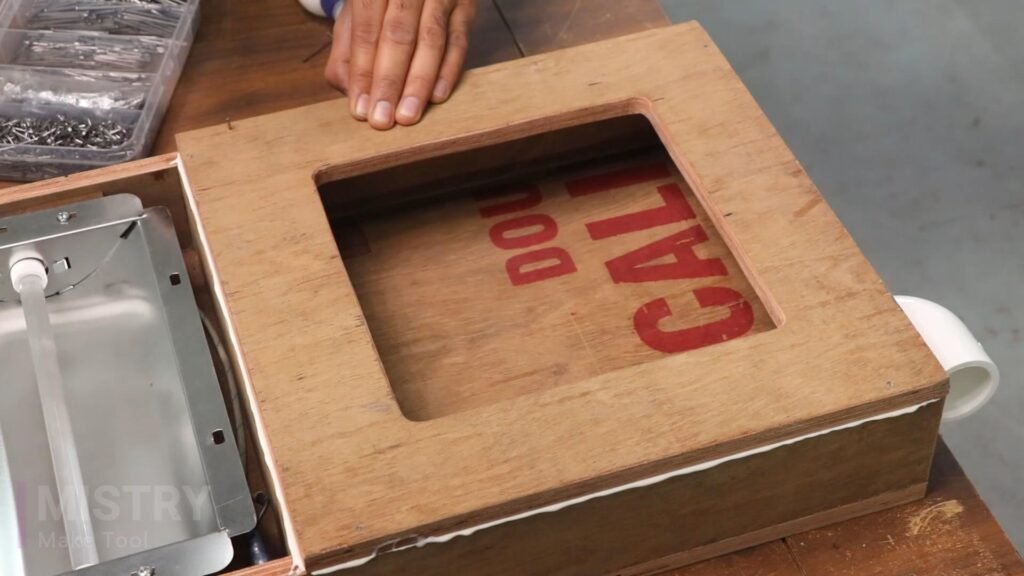
Drill many small holes in the top surface of the box for the vacuum chamber. This top surface will be where the mold will be placed, and the holes will allow the vacuum to pull the air through.
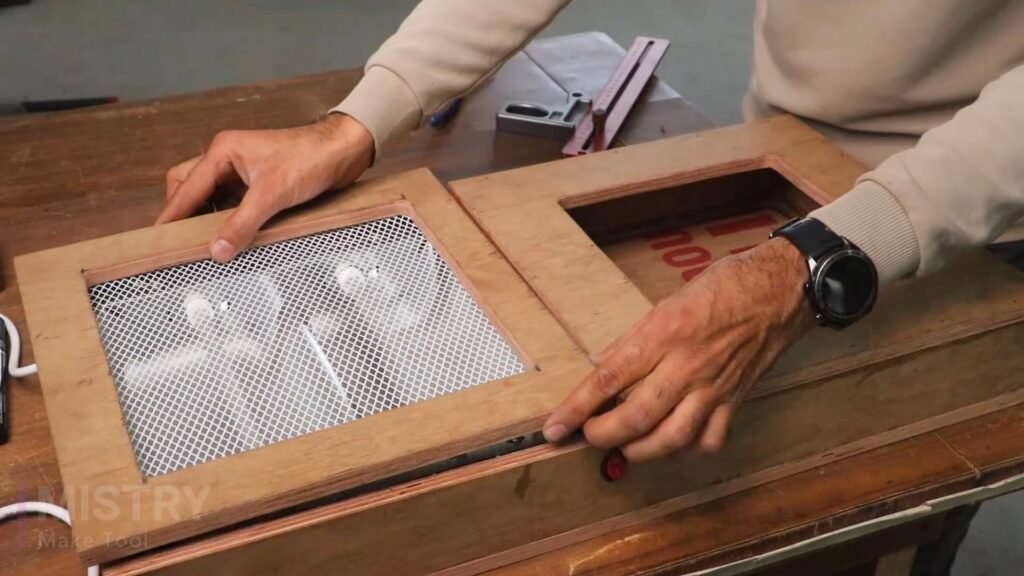
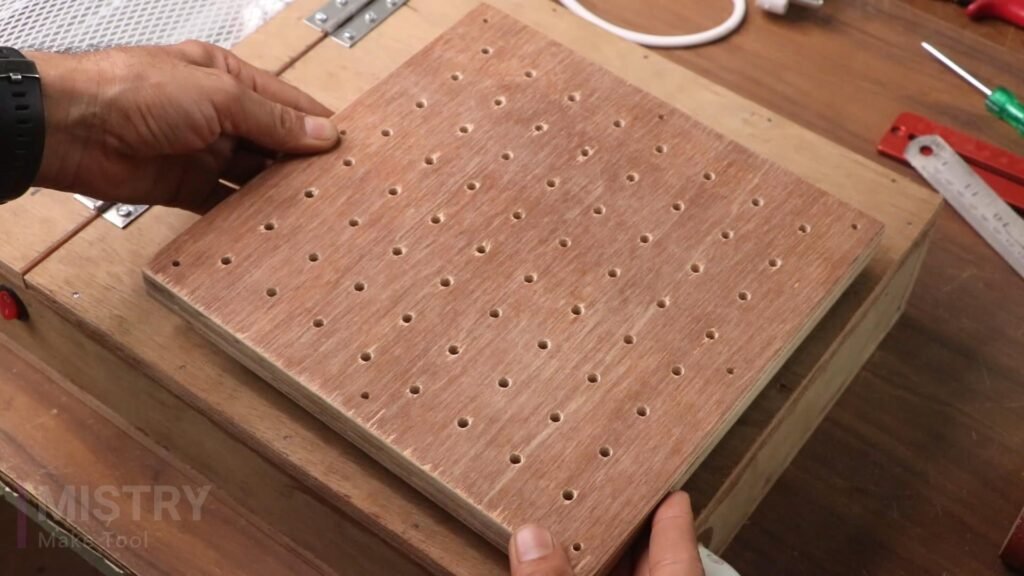
Also place the safety net on the top of the heating frame structure.
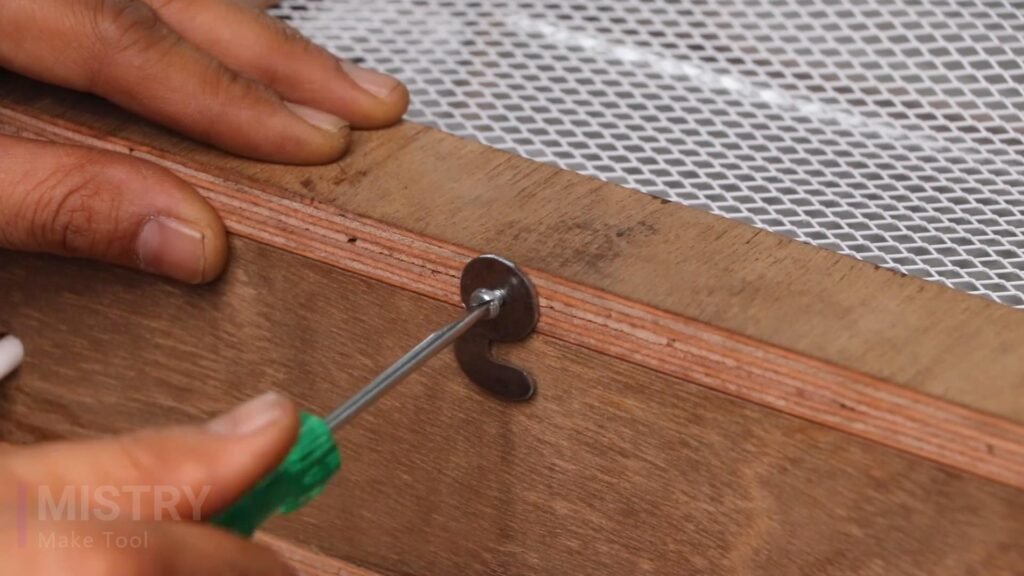
4. Create the Plastic Sheet Holder:
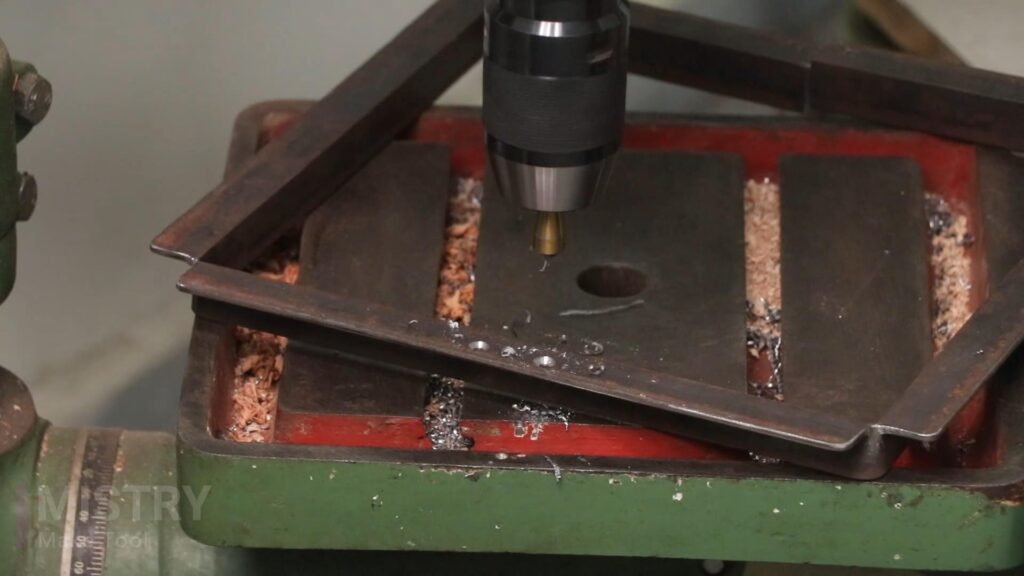
Construct two identical frames using L-angles. These frames should be slightly smaller than the plastic sheets you intend to use.
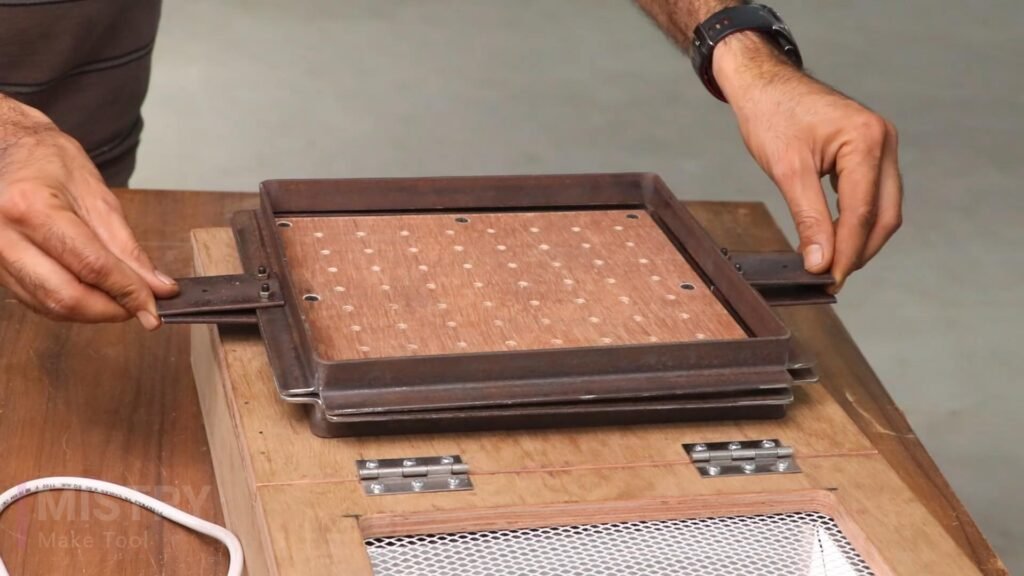
These two frames will clamp together using 6mm knobs, holding the plastic sheet securely between them.
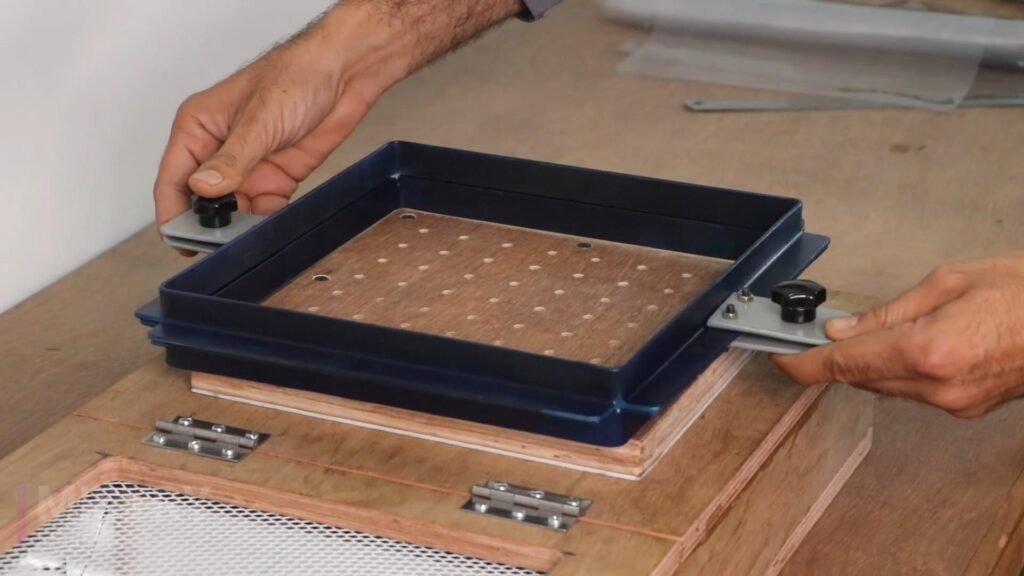
5. Prepare for Operation:
Place the mold on the perforated top surface of the vacuum chamber.
Place a plastic sheet between the L-angle frames, and clamp them together.
Connect the vacuum cleaner hose to the hole in the vacuum chamber.
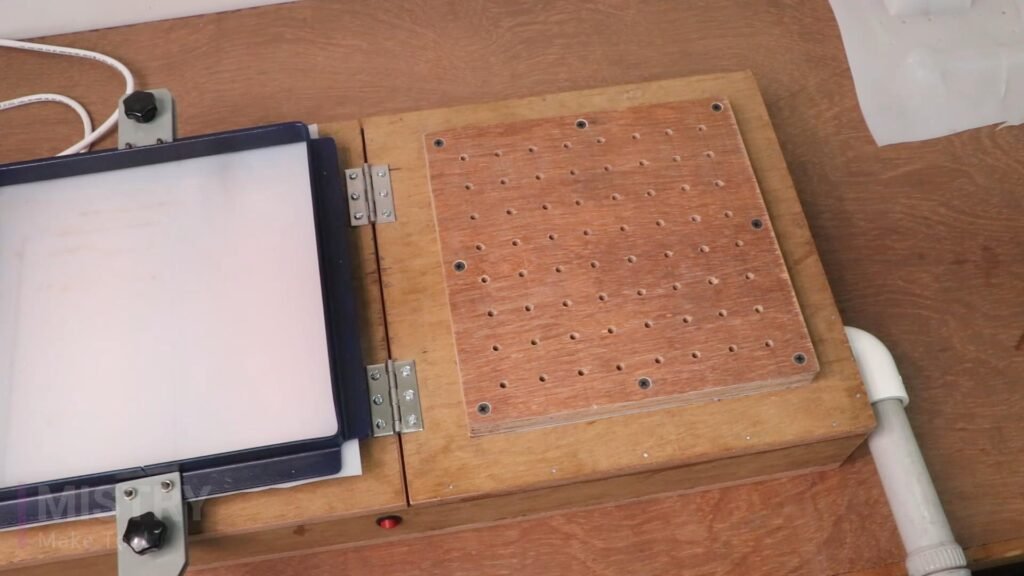
6. Vacuum Forming Process:
Turn on the heating unit and position the plastic sheet holder beneath it. Heat the plastic sheet until it becomes soft and pliable.
Move the plastic sheet holder unit onto the mold.
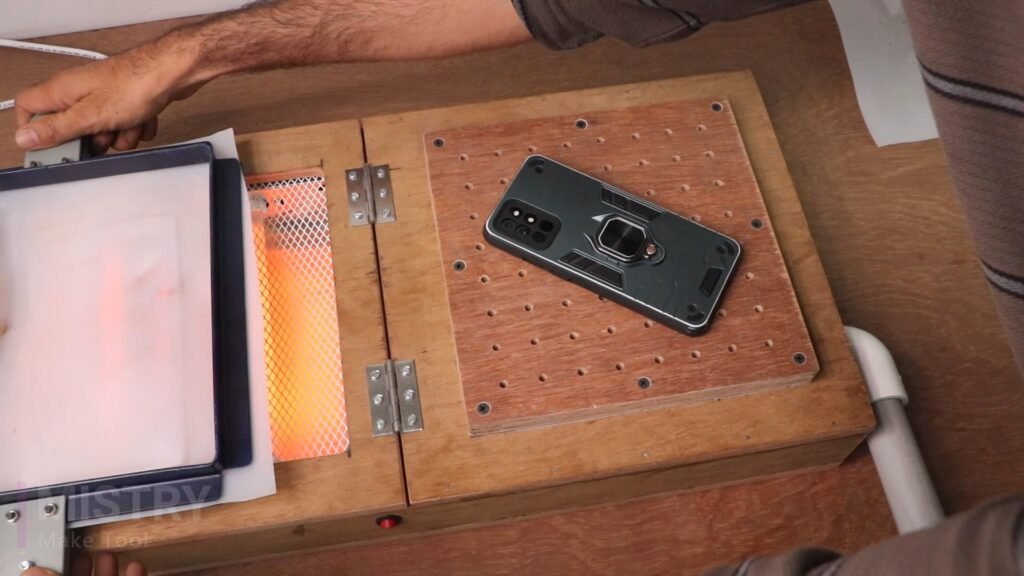
Turn on the vacuum cleaner, which will draw the plastic sheet down onto the mold.
Allow the plastic to cool and solidify before removing it from the mold.
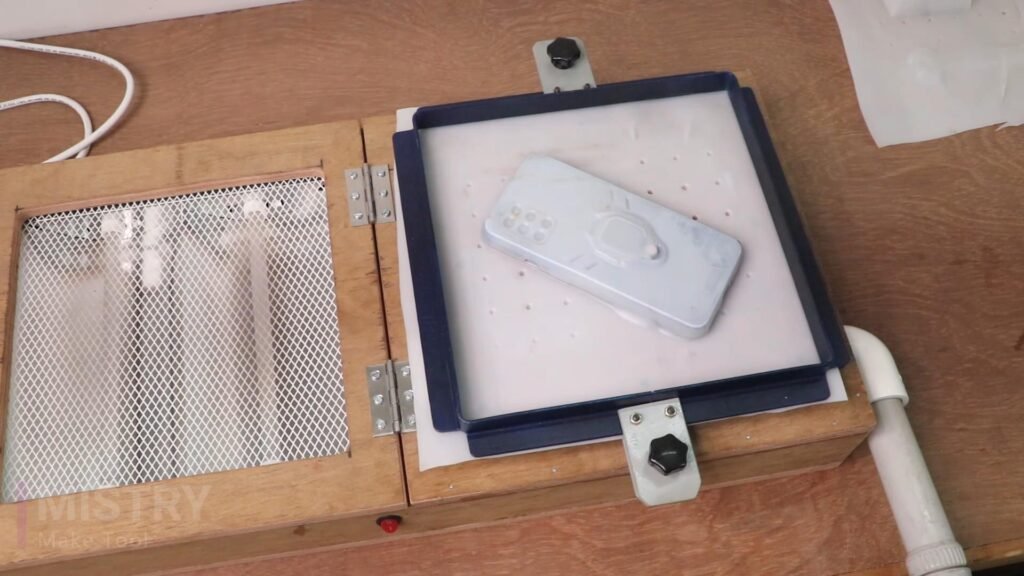
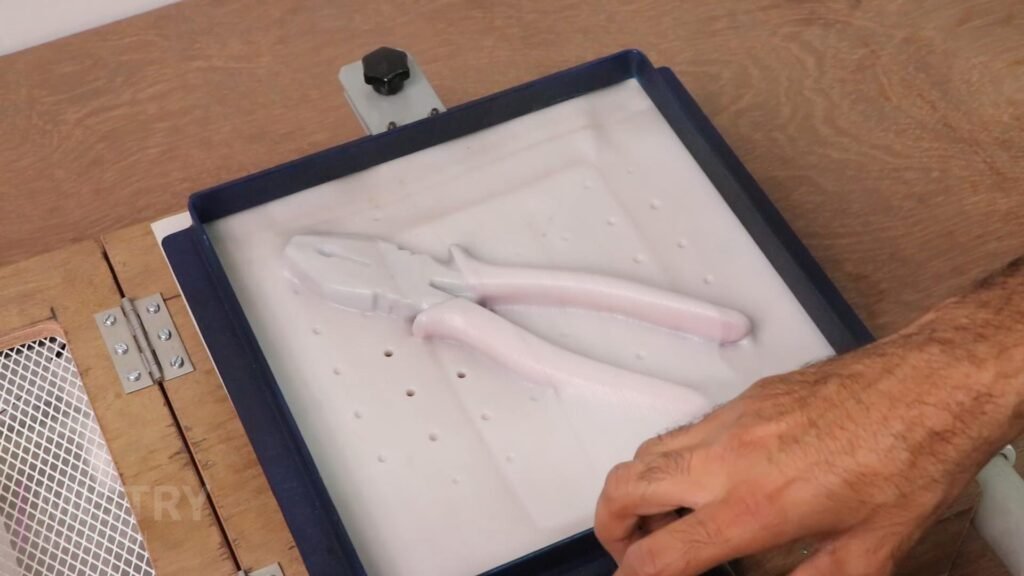
Important Safety Considerations:
- Electrical Safety: Exercise extreme caution when working with electrical components. Ensure all connections are secure and properly insulated.
- Heat Safety: The heating tube generates high temperatures. Keep flammable materials away and wear heat-resistant gloves.
- Ventilation: Ensure adequate ventilation when operating the machine, as some plastics can release fumes when heated.
- Adult supervision: This project should be undertaken with adult supervision.