
INTRODUCTION :
A hydraulic press is a machine using a hydraulic cylinder to generate a compressive force. It uses the hydraulic equivalent of a mechanical lever. A hydraulic press is a machine that has a plate in which the metallic material is placed so that it can be crushed, straightened or moulded. Unlike their mechanical counterparts, hydraulic press machines can compress any material to a full extent. Also, hydraulic presses take only half of the space that the mechanical ones take because they have the ability to compress a large pressure in a cylinder having a less diameter.
Hydraulic presses are commonly used for forging, clinching,moulding, punching, deep drawing, and metal forming operations. With the growth and importance of light-weighting in the aerospace and automotive industry, more applications are present in Thermoplastics, Composites, RTM Resin Transfer Molding, GMT Glass Mat Transfer and Carbon Fiber Molding. All of these applications require precise control and repeat-ability.
An industrial sized hydraulic press machine is extremely heavy and expensive, but a smaller version can be made using a standard 5 ton bottle jack—the same type used to change a car tire. A blast shield and safety glasses should always be used when crushing anything, especially if it’s hard material.
Parts Used :
- L-Section angle heavy (2”*2”)
- Square pipe heavy (1½”*1½”)
- 2 Nos. spring
- 5 Ton hydraulic jack
- Tractor trolly pin heavy
- 12 Nos. M10 bolts ( 2½” length) with nuts
- 2 Nos. M10 bolts (3” length) with nuts
- 2 Nos. M10 allenky bolts (1” length)
- 4 Nos. M8 allenky bolts (½” length)
- 2 Nos. 3/8 allenky bolts (½” length)
- 4 Nos. ¼ allenky bolts (½” length)
- 3/8 Bolt (1¼” length)
- 2 Nos. 5/16 J bolt (2½” length) with nuts
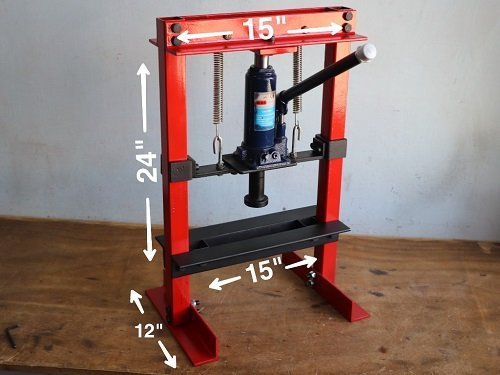
How to make :
Step 1 :- Cutting of parts
First step to make a hydraulic press is cutting of required metal parts. So, I cut everything to its proper length and dimension such as L-section angle, square pipe etc. Then next step is drilled a holes for proper assembly of all cutting metal parts to make a frame of hydraulic press.

For cutting and drilling of parts you must ensures the safety protection. A pair of work gloves is good insurance against a wire brush if it should slip, as well as cutting down on the vibration being transmitted to your hands.

With that in mind, eye and hearing protection is a must. An angle grinder with a cut off blade makes a racket which soon causes a ringing in the ear without proper protection, it also sprays a shower of sparks which can bounce back off nearby objects, beware the hot spark bouncing back off a wall over the top of your safety goggles, it’s not a fun experience.
Step 2:- Assembly of all metal parts
Second step is assembly of all cutting metal parts. I assembled all the metal parts without any kind of welding. I only used bolts and nuts for proper assembly of metal parts to make a frame of the hydraulic press.

Proper assembly to make a frame body of the hydraulic press is shown in the image.
Step 3:- A 5 ton bottle jack and springs
I used 5 ton bottle jack to make this hydraulic press. Also I used 2 mechanical springs to allow the hydraulic jack in its first position. Both the hydraulic jack and springs are attached with the frame by using of bolts. Springs are attached by using of J bolts.

For better look I painted it with black and red colours.
Step 4:- Testing

Now, this machine is ready to use. A hydraulic press is a machine that has a plate in which the metallic material is placed so that it can be crushed, straightened or moulded. In this machine you can easily straightened and crushed metal parts.
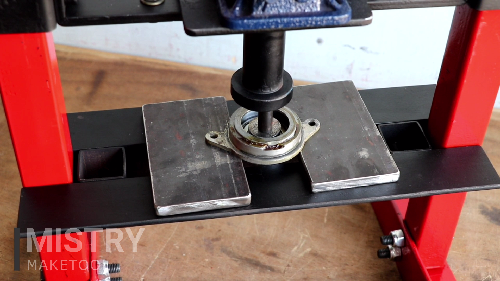